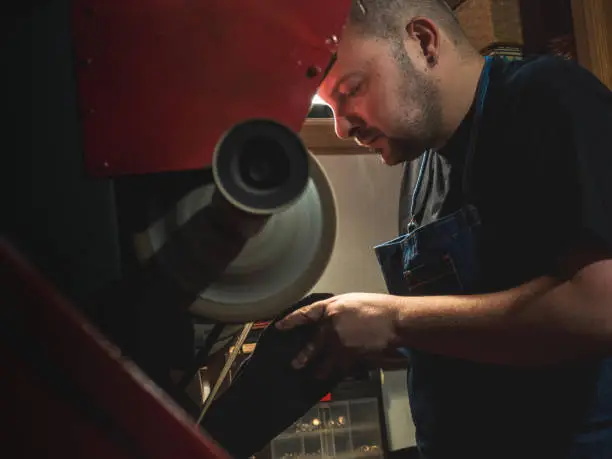
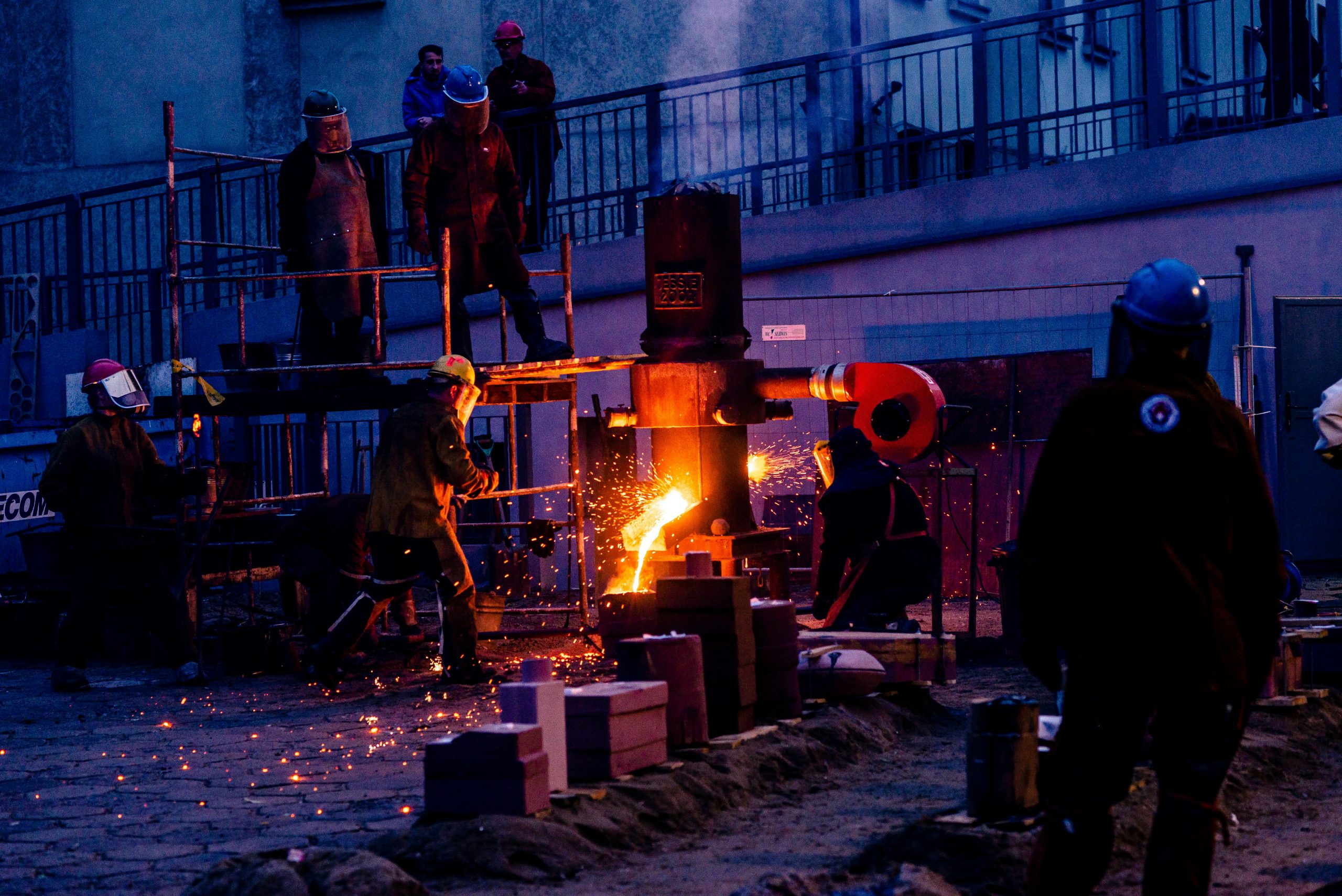
How does metal spinning compare to other forming techniques?
Metal spinning is just one option when it comes to modern metal forming techniques. However, as with most technical solutions, there are many techniques and processes that can be used to get the results you want. Businesses that need metal parts therefore need to do research to establish which technique is right to support their operations or complete a particular project. In this post, we’ll be going into detail on the other forming techniques that are out there and how they compare to metal spinning.
What techniques can be used to form metal?
There are many different metal fabrication techniques that can be employed to produce precision metal parts. However, each of these processes has its own pros and cons depending on the priorities of the business. Other than metal spinning, the main alternative techniques for forming metal include the following.
As the name suggests, hydroforming involves shaping metal using a pressurised fluid in conjunction with a mould. This technique is typically used for materials with a high ductility, such as aluminium, copper, and steel. The main benefit of hydroforming metal is that it can easily achieve irregular shapes and implement complex designs. It is also very accurate, as it causes minimal thinning of the material. However, the production time per part can be longer and costs can be higher when using hydroforming compared to other forming techniques.
This metal forming process sees the material stock passed between two mechanical rollers which apply pressure to the metal. This causes the metal to deform and become thinner. Rolling can be either a hot or cold process, with heat often being an addition that’s necessary to form tougher materials. Rolling is typically considered as a technique used in the early stages of production to get the metal to the right thickness or making bends in the metal. This is because rolling is somewhat limited in the metal shapes it can achieve.
During the process of metal stamping, the material is cut, bent, and then pressed onto a die. Stamping is designed for the mass production of simple shapes with straight edges.
Molten metal is poured or injected into a specially made mould cavity. As the metal cools, it takes on the shape of the mould. This technique is effective at created complex shapes with varied edges in one quick step. The main negative is that it can be very expensive to create the moulds and the process of heating the metal is very energy intensive. In addition, there is limited scope to make adjustments to the casting process if something goes wrong.
Metal press forming shares some similarities with stamping, except with more flexibility in the shapes that can be made. A hydraulic metal press can form cones, cylinders, rectangles, and more in a range of sizes. The largest press in the Tanfield facility has a bed size of 1200 x 1500mm and a drawing depth of 650mm.
How does metal spinning compare?
Metal spinning is an extremely versatile forming technique that’s able to achieve a high level of accuracy and produce large volumes of parts efficiently. Metal spinning produces precision symmetrical shapes using a spinning lathe and tools, overseen by a skilled operator. You can learn more by reading ‘What is the metal spinning process?’. The benefits of spinning metal include:
- Ability to use a wide range of materials.
- Process repeatability.
- Strengthens parts due to lack of heat and seam.
- Low material costs.
- Large production volume.
- Flexibility allows changes to be made to part design and realised.
Ultimately, the right metal forming technique for your business will depend on a number of factors. This includes the materials being used, the production volume, part geometry, and project budget. However, metal spinning serves as the best all-round option. It can easily be combined with other similar techniques such as swaging or joggling to create more complex shapes. Furthermore, bespoke metal spinning services are available to meet unique sector requirements.
Large scale metal spinning UK
Using Tanfield Metal Spinners has the added benefit of low tooling costs. This is due to the fact that we have the largest stock found anywhere in the UK. Get in touch through our website or by calling to get a fast quote on the work you need done.